TSMC Uses AMD's EPYC Chips to Make Chips
The silicon Ouroboros
TSMC produces chips for AMD, but it also now uses AMD's processors to control the equipment that it uses to make chips for AMD (and other clients too). Sounds like a weird circulation of silicon, but that's exactly what happens behind the scenes at the world's largest third-party foundry.
There are hundreds of companies that use AMD EPYC-based machines for their important workloads, sometimes business-critical workloads. Yet, when it comes to mission-critical work, Intel Xeon (and even Intel Itanium and mainframes) rule the world. Luckily for AMD, things have begun to change, and TSMC has announced that it is now using EPYC-based servers for its mission-critical fab control operations.
"For automation with the machinery inside our fab, each machine needs to have one x86 server to control the operation speed and provision of water, electricity, and gas, or power consumption,” said Simon Wang, Director of Infrastructure and Communication Services Division at TSMC.
“These machines are very costly. They might cost billions of dollars, but the servers that control them are much cheaper. I need to make sure that we have high availability in case one rack is down, then we can use another rack to support the machine. With a standard building block, I can generate about 1,000 virtual machines, which can control 1,000 fab tools in our cleanroom. This will mean a huge cost saving without sacrificing failover redundancy or reliability."
TSMC started to use AMD EPYC machines quite some time ago for its general data center workloads, such as compute, storage, and networking. AMD's 64-core EPYC processors feature 128 PCIe lanes and support up to 4TB of memory, two crucial features for servers used to run virtual machines. But while the infrastructure to support 50,000 of TSMC's employees globally is very complex and important (some would call it business-critical), it isn't as important as TSMC's servers that control fab tools.
Fab tools cost tens or hundreds of millions of dollars and process wafers carrying hundreds of chips that could be used to build products worth tens of thousands of dollars. Each production tool uses one x86 server, or at least a virtual server. Sometimes hardware fails, so TSMC runs its workloads in such a way that one server can quickly replace the failed one. (Naturally, TSMC does not disclose which operating systems and applications it runs at its fabs.)
At present, TSMC uses HPE's DL325 G10 platform running AMD EPYC 7702P processors with 64 cores (at 2.0 GHz ~ 3.35 GHz) in datacenters. It also uses servers based on 24-core EPYC 7F72s featuring a 3.20 GHz frequency for its R&D operations. As for machines used in TSMC's fabs, the foundry keeps their specifications secret.
It is noteworthy that AMD's data center products are used not only to produce chips, but also to develop them. AMD's own Radeon Technologies Group uses EPYC processors to design GPUs.
Get Tom's Hardware's best news and in-depth reviews, straight to your inbox.
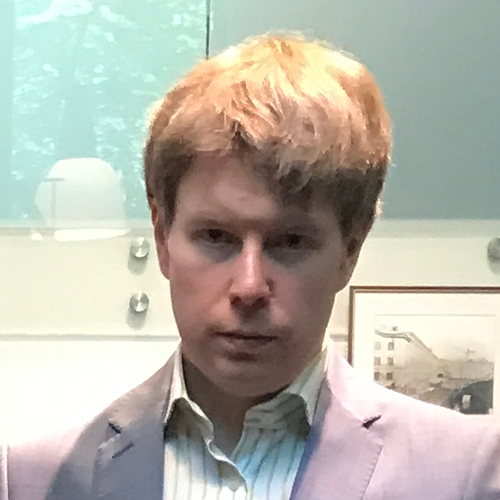
Anton Shilov is a contributing writer at Tom’s Hardware. Over the past couple of decades, he has covered everything from CPUs and GPUs to supercomputers and from modern process technologies and latest fab tools to high-tech industry trends.
-
InvalidError There is nothing weird about having a circular manufacturing chain where stuff you make ultimately gets used to help you make more better stuff. Workshops often need to make custom tools for a job or even make the custom tools needed to make custom tools for a job. For robots and multi-axes machining, high-precision machines get gilded and used to make higher-precision parts in order to make even higher precision machines possiblem, rinse and repeat until you have reached the desired level of precision or the practical limits within a given budget.Reply
Practically all industries where the machines can be used to improve themselves in some way have a circular element to it. -
Kamen Rider Blade It's great that TSMC uses their own Fabricated CPU's for their Server Infrastructure.Reply -
sreams InvalidError said:There is nothing weird about having a circular manufacturing chain where stuff you make ultimately gets used to help you make more better stuff. Workshops often need to make custom tools for a job or even make the custom tools needed to make custom tools for a job. For robots and multi-axes machining, high-precision machines get gilded and used to make higher-precision parts in order to make even higher precision machines possiblem, rinse and repeat until you have reached the desired level of precision or the practical limits within a given budget.
Practically all industries where the machines can be used to improve themselves in some way have a circular element to it.
I suppose what makes this a little different is the fact that these are not custom tools. It just so happens that the product TSMC manufactures for a customer is a good fit for their needs. I suspect that doesn't happen all that often. -
InvalidError
It likely happens 24/7, just not with parts people can be bothered to know about. Each ASML machine probably has 100+ micro-controllers, SoCs, DSPs, FPGAs, CPLDs, etc. made in TSMC fabs and many more made elsewhere. Everyone has dependencies with everybody else.sreams said:I suppose what makes this a little different is the fact that these are not custom tools. It just so happens that the product TSMC manufactures for a customer is a good fit for their needs. I suspect that doesn't happen all that often.
If you think 100 processors of some sort is a lot for a 100 tons wafer-processing machine that is in charge of managing wafer exposure at sub-nanometer precision, keep in mind that modern cars where nearly everything is controlled by wire to some extent can have 200+. -
Co BIY I'm pretty sure that if you searched the TSMC plant you would find IC tech from nearly every company worldwide that makes it.Reply
AMD is a bigger customer to TSMC than Intel but Intel accounted for ~8% of revenue IIRC.
On the other hand this is probably another step towards Skynet. -
sreams InvalidError said:It likely happens 24/7, just not with parts people can be bothered to know about. Each ASML machine probably has 100+ micro-controllers, SoCs, DSPs, FPGAs, CPLDs, etc. made in TSMC fabs and many more made elsewhere. Everyone has dependencies with everybody else.
If you think 100 processors of some sort is a lot for a 100 tons wafer-processing machine that is in charge of managing wafer exposure at sub-nanometer precision, keep in mind that modern cars where nearly everything is controlled by wire to some extent can have 200+.
What you are referring to is specific to TSMC. I'm simply saying that most manufacturing companies probably don't use their clients' products all that often. As in... whomever makes that plastic chair for IKEA, or whomever makes the turn signal switch in your car. I was also addressing your point about custom tools. Obviously EPYC chips used in TSMC's servers are not custom made for that application. -
Gomez Addams
Who said there is a problem?lvt said:I don't see problem here, as long as they paid for it 😁 -
lvt Gomez Addams said:Who said there is a problem?
The article itself has no problem, but the title is a bit misleading.