The world's semiconductor industry hinges on a single quartz factory in North Carolina
The deposits formed 380 million years ago when Africa collided with North America.
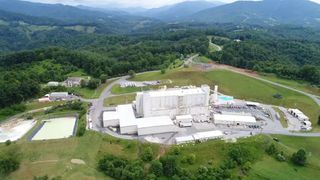
A Wharton professor who studies AI, innovation, and start-ups dramatically claims that "the modern economy rests on a single road in Spruce Pine, North Carolina." Ethan Mollick explains that this unremarkable road leads to a Sibelco North America Inc. facility where ultra-high-purity quartz is mined. This location is vitally important as it is claimed to be "the sole supplier of the quartz required to make the crucibles needed to refine silicon wafers."
The modern economy rests on a single road in Spruce Pine, North Carolina. The road runs to the two mines that is the sole supplier of the quartz required to make the crucibles needed to refine silicon wafers.There are no alternative sources known. From Conway’s Material World: pic.twitter.com/mYfrfub8dwMarch 9, 2024
Regular readers will be well aware of several vital companies and locations that sustain the semiconductor industry as we know it. We have published numerous articles about Intel, TSMC, ASML, Samsung, and other companies. Moreover, locations such as Silicon Valley, Hsinchu Science Park, Bengaluru, and the Shenzhen SEZ have become household names due to their tech hub status. Put into this perspective, the remarkable nature of Spruce Pine is all the more eyebrow-raising.
Mollick provides an excerpt from Conway's Material World, which discusses the probable "end of computer chip manufacture as we know it," should something untoward happen at Spruce Pine or in the skies above it.
For further insight into why the Spruce Pine location is so unique, the official Sibelco pages do a pretty good job of encapsulating the story of this particular mine. It is the world’s leading high-purity quartz (HPQ) provider, and the firm claims it produces “the world’s highest quality quartz” at this mine.
Geologically speaking, the uniquely pure minerals at Spruce Mine were created about 380 million years ago when Africa collided with North America. This momentous collision, however slow, caused intense friction and heat miles below the Earth’s surface. According to Sibelco, the Spruce Mine minerals were created by a rich mineral-forming liquid that cooled and crystallized over time. A standout feature of these minerals is that they were made in their purest forms due to a lack of water, which caused all the friction.
In more recent history, it is claimed that the Spruce Pine site has been mined for centuries, with Native American peoples known to have mined Mica. In addition to Mica and the headlining HPQ, the mine is a rich source of kaolin and feldspar.
Spruce pine-sourced minerals were first used for electronics by Thomas Edison, who used Mica as an insulator in some of his inventions as far back as 1879.
Stay On the Cutting Edge: Get the Tom's Hardware Newsletter
Get Tom's Hardware's best news and in-depth reviews, straight to your inbox.
The fused quartz from Spruce Pine HPQ offers “unparalleled optical, mechanical, and thermal properties” for semiconductors, solar photovoltaic cells, optical fiber, and quartz lighting.
Returning to the question of Spruce Pine's particular importance, Mollick makes it clear in his social media thread that, yes, fully synthetic techniques are available to create similarly pure quartz. However, any sudden closure or interruption of the mining at Spruce Pine would likely cause "pretty catastrophic" disruption (and extra expense) for a few years as the industry scales up manufacturing.
Mark Tyson is a news editor at Tom's Hardware. He enjoys covering the full breadth of PC tech; from business and semiconductor design to products approaching the edge of reason.
-
Blastomonas This is either a great idea for their share prices or bad marketing for terrorists.Reply -
bit_user
That aspect does worry me. Then again, if no one is aware that such a single point of failure exists, there's less chance of redundancies being added. So, it can be a bit of a catch-22.Blastomonas said:This is either a great idea for their share prices or bad marketing for terrorists.
It turns out lots of industries have such bottlenecks in their supply chain, and we rarely discover them until something goes wrong. I remember there was a fire at a plant which produced the specialized plastic used in automotive brake lines, and it was estimated to stay offline for a couple years for all the necessary repairs. It turned out that one plant served like 60% of the market, leading to fears that fewer cars could be shipped due to an inability to simply outfit them with brake lines. I never heard whether it did finally affect automotive production or whether enough other production capacity could be shifted to meet demand. Probably, the fact that I didn't hear more about it says that the industry managed to cope better than expected. -
USAFRet This is similar to pool chlorine a couple of years ago.Reply
There were apparently only 3 factories in the US that made pool chlorine.
One of them burned down.
Result - Immediate freakout, price spike, and short term shortages.
This quartz mine is worse, because it appears to be a single source. -
zanfarix I do not believe this to be entirely true. The silica is mined at Spruce Pines, but it's refined to it's final purity in Norway. Before the silica was shipped in to Norway the plant used local sources for ultra pure quartz and Norway is rich in pegmatites. Most value chains today are driven by cost cutting until there only remains the few which are the most profitable. There often are several dormant sources that can be tapped if the market shifts. The failure of a plant or source to deliver always creates delays, but a complete collapse seems rare if not unprecedented.Reply -
bit_user
The article did acknowledge that alternate sources could be scaled up, but that takes time. Recall that semiconductor manufacturing is a high-volume business, very capital-intensive, often "just-in-time", and often operating very near peak capacity. If silicon supply were suddenly cut to a fraction, I have no doubt that the implications for fabs and their various downstream customers would be fairly catastrophic, even out to the mid-term time frame. I think we could anticipate it being much worse than what we experienced, during the pandemic era supply crunch.zanfarix said:The failure of a plant or source to deliver always creates delays, but a complete collapse seems rare if not unprecedented.