TSMC Arizona struggles to overcome vast differences between Taiwanese and US work culture
Worker treatment that's acceptable in Taiwan simply won't be tolerated by US employees
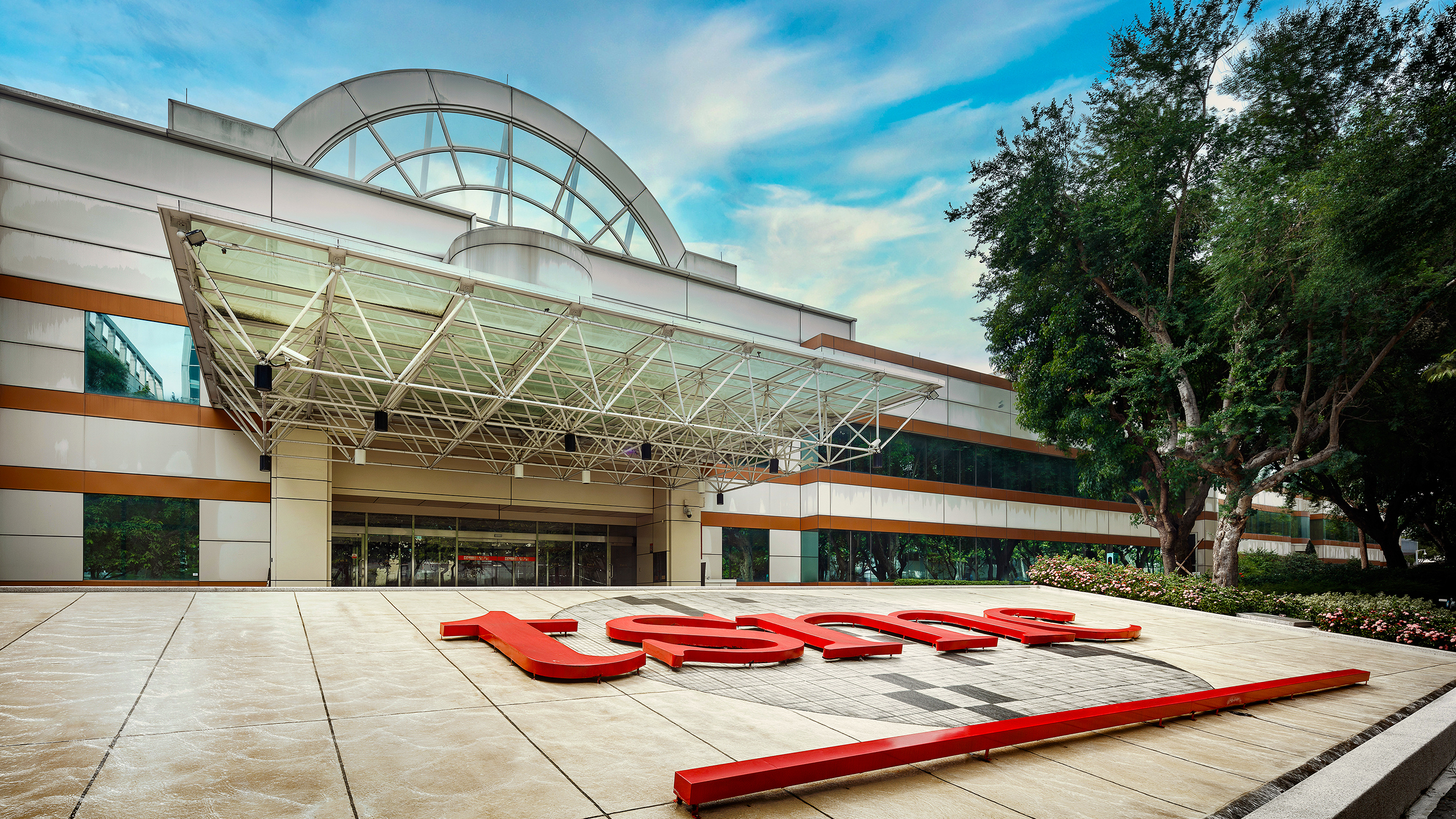
Taiwan Semiconductor Manufacturing Company (TSMC), one of the world’s largest advanced computer chip manufacturers, continues finding its efforts to get its Arizona facility up and running to be more difficult than it anticipated. The chip maker’s 5nm wafer fab was supposed to go online in 2024 but has faced numerous setbacks and now isn’t expected to begin production until 2025. The trouble the semiconductor has been facing boils down to a key difference between Taiwan and the U.S.: workplace culture. A New York Times report highlights the continuing struggle.
One big problem is that TSMC has been trying to do things the Taiwanese way, even in the U.S. In Taiwan, TSMC is known for extremely rigorous working conditions, including 12-hour work days that extend into the weekends and calling employees into work in the middle of the night for emergencies. TSMC managers in Taiwan are also known to use harsh treatment and threaten workers with being fired for relatively minor failures.
TSMC quickly learned that such practices won’t work in the U.S. Recent reports indicated that the company’s labor force in Arizona is leaving the new plant over these perceived abuses, and TSMC is struggling to fill those vacancies. TSMC is already heavily dependent on employees brought over from Taiwan, with almost half of its current 2,200 employees in Phoenix coming over as Taiwanese transplants.
The move to begin manufacturing chips in Arizona was seen as one way to boost advanced chip-making in the U.S. and reduce reliance on Taiwan imports. Given rising tensions between the United States, China, and Taiwan, this is considered to be of vital importance. U.S. Commerce Secretary Gina M. Raimondo says the country purchases 92 percent of its most advanced chips from Taiwan.
TSMC has committed $65 billion to the project, The New York Times notes. Furthermore, the facility has a $6.6 billion grant from the U.S. government under the CHIPS and Science Act.
The plan is to create 6,000 jobs as TSMC builds out the rest of the facility. Ultimately, TSMC will have three different factories at its Phoenix campus, and it desperately wants to reduce the ratio of Taiwanese immigrants to local hires.
“We want to make this site a successful site and a sustainable site,” according to Richard Liu, director of employee communications and relations at the Arizona site. “Sustainable means that we cannot keep relying on Taiwan sending people here.”
Get Tom's Hardware's best news and in-depth reviews, straight to your inbox.
In response to an uptick in engineering positions at TSMC and elsewhere, nearby colleges and universities have increased their curriculum in fields like electrical engineering. TSMC has collaborated in many of these programs with apprenticeships, internships, research projects, and career fairs. It’s also working with colleges and tech-oriented high schools to build clean rooms, the heart of semiconductor manufacturing, to give students exposure to the environments.
To help deal with the culture clash, TSMC has been sending U.S. employees to Taiwan to observe the Taiwanese way. At the same time, the chipmaker is putting its managers through communications training to help them better work with U.S. employees.
If TSMC is going to succeed with its Arizona chip-making venture, it needs to come to terms with the fact that it’s not the only game in town there. While TSMC is considered by many in Taiwan as the pinnacle of engineering jobs, other companies in Arizona are competing for that labor pool. Intel, in particular, is expanding its Arizona chip factory.
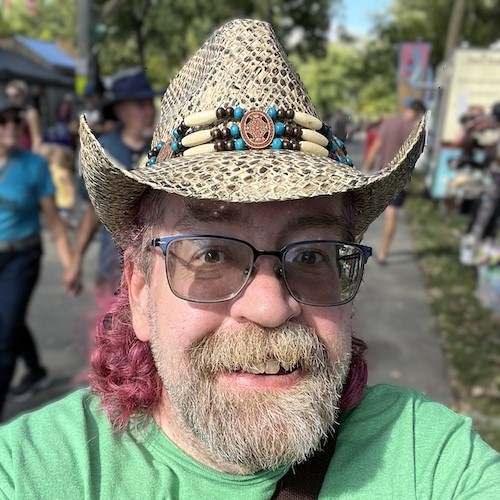
Jeff Butts has been covering tech news for more than a decade, and his IT experience predates the internet. Yes, he remembers when 9600 baud was “fast.” He especially enjoys covering DIY and Maker topics, along with anything on the bleeding edge of technology.
-
parkerthon Makes me wonder what the solution is here. Obviously Japan’s working culture was aggressively different initially during 80’s, but they managed to mostly bridge the culture gap and found good results learning to manufacture in the US. Sounds to me like TSMC are literally importing half their work force to grind this process forward instead of stepping back to ensure they connect with US norms and culture before they start things up. Sounds like TSMC doesn’t have anyone with any experience building a global company frankly.Reply -
jp7189 TSMC is the pride of Taiwan. It's an honor to work there. Kids plan their classes with the goal of landing a job there.Reply
Literally zero people dream of working at TSMC Phoenix. It's just one of many options to pay the bills where the least amount of work for the highest pay is a chief consideration. -
rluker5 There are a lot of good workers in the US, but also a lot of terrible workers.Reply
Often the terrible workers, who do as little as possible without getting fired, are good at looking like they are not terrible unless you work with them and have to clean up/ finish up/ fix/ preemptively take specific actions so they don't ruin the product. It becomes obvious then, especially when you have equipment that keeps a history of what was done with it.
If you don't have experience dealing with these Homer Simpsons because they are rare where you come from you might wind up with a lot of them. -
hotaru251
If TSMC is going to succeed with its Arizona chip-making venture, it needs to come to terms with the fact that it’s not the only game in town there. While TSMC is considered by many in Taiwan as the pinnacle of engineering jobs, other companies in Arizona are competing for that labor pool. Intel, in particular, is expanding its Arizona chip factory.
dumb take imo.
Intel's fab can't do what TSMC can....else there wouldnt be a need for US to give funding to TSMC to begin with.
While yes the culture difference is a thing I don't blame TSMC for doing it their way...they got to be where they are doing exactly that.
As an American I also understand nobody wants to work more than needed but I am pretty sure these terms are in contact/info for the job....a job they agreed to terms of....If they didn't like it why did they bother accepting job? -
Overfloating I gladly left the SC industry behind after 5 years in a coveted "Process Integration Engineer" role, basically the bullies of the process side of the fab. Although I did not work for TSMC (and never will) I faced the same issues that all people that aren't actually androids in the industry eventually face and cope with in their own ways: burnout. The 24/7 nature of the industry meant that even when you're off work you aren't actually off work, you constantly have the specter of being called any time of the day/weekend, possibly even on vacation. It wears on you. Management's reply was that "this is the industry" which is basically all I've read from TSMC's side regarding their problems in the USA. I have no problem putting in a solid 8 hour day but especially in critical roles that is the minimum expectation. I didn't pour YEARS of my life in school getting a post graduate degree to be treated like a slave with a paycheck. If people have other options, in this country, they take them. The Phoenix area also has plenty of aerospace jobs available for electrical engineers so if TSMC thinks they are going to ride in on their reputation as being the #1 manufacturer in the world of SCs and expect hires to constantly fellate them when they treat their workers like crap, well, get ready for a reality check suckers! I laugh every time I read articles like this knowing I made the right choice to leave the industry and their mostly clueless management behind and focus on gaining skills with my hands, which will always be in demand and gives me the freedom over my precious time on this earth. My suggestion to TSMC is this, treat your Taiwanese workers like slaves if that works for you over there, but this is America, we won't put up with your BS and getting fired by a tyrant isn't a scary thing for a well educated person with options. You have less power over here so you better make a massive culture adjustment to your US operations or you will continue to face delay after delay due to turnover of your newly trained workers. If you call yourselves the masters of efficiency prove that you're also adaptable because you sure as hell aren't efficient at all when you can't treat your employees like slaves. Oh yeah and if you're looking for anyone with experience in PI, don't call me!Reply -
DS426
Yeah, ok, glad you got that out. Fortunately or unforunately, it's true.hotaru251 said:dumb take imo.
Intel's fab can't do what TSMC can....else there wouldnt be a need for US to give funding to TSMC to begin with.
While yes the culture difference is a thing I don't blame TSMC for doing it their way...they got to be where they are doing exactly that.
As an American I also understand nobody wants to work more than needed but I am pretty sure these terms are in contact/info for the job....a job they agreed to terms of....If they didn't like it why did they bother accepting job?
If any other internal corporation could just come into the U.S. and do what the F ever they wanted to, then yeah, competition be darned and they're the winner of the universe. That's just not how it works.
The reports said that engineer and other job types didn't expect to be working the long hours that they are and travel just getting spun up on the job. I think the problem is that the contract leaves room for that over-time and on-call nature with zero regret for personal life circumstances, like health, families, etc. That might be how Taiwan works, but in the U.S., we're at least allowed to put our families, our country, our faith first. That's not an option at TSMC, and it's being learned the hard way.
So that's really where it's at. If you want to commit to the TSMC/semiconductor cult, it's there for good pay and "purpose." Otherwise, you're apparently a sh*tbag and not contributing sufficiently to their crazy success.
Completely off on the U.S funding thing as it applies to everyone equally and is about national supply chain and "national defense" -- Samsug gets funding, Intel gets funding, TSMC gets funding, Micron gets funding, and at least a half dozen other small orgs get funding to INCENTIVIZE chip production in the U.S. The difference is that if TSMC thought that they could invoke the same labor conditions here... *mind blown* lesson learned, lol. I don't feel bad for them because life is more than working... just my opinion. -
JamesJones44 I keep seeing this about TSMC, but makes me wonder why Samsung hasn't had any issues yet. It's early in the process so maybe the will pop up, but thus far Samsung hasn't been complaining about culture differences. Maybe this is more of a TSMC issue they are trying to pass off instead of owning. I guess well see in a few months how the Samsung plant in Taylor Texas progresses.Reply -
JRStern With a $65+ billion budget I hope somebody expected these problems and has plans to deal with them, but I'm also sure they are very real. There's a culture thing, for sure. I suspect a much bigger problem is going to be a competence problem, and poorly qualified workers only aggravate the culture gaps. Being an engineer in the US has lost status in the US over the last generation. It attracts fewer people and less well qualified. And every one wants to quit the big company and start their own to get the big bucks. Plus I don't doubt there is a second culture gap, the Taiwanese thinking all the Americans are a step down or they wouldn't need Taiwan to come to their rescue. That may be true or false in reality but that will not fly with Americans, at all. The problem could continue.Reply -
overlord Makes one wonder how Amazon, Tesla and X get away with similar working environments 🤫Reply